Which is easier to trust -- a 1,300-component assembly with shaky performance, or a 10-component one with reliable data?
Many manufacturers have worked with the standard, stamped lamination steels for decades. Engineers know the obstacles associated with them, and they accept them as law. But the emergence of powder-based soft magnetic materials shouldn't be ignored by those looking to increase their electric motor's efficiency.
Those seeking a truly unique, remarkable part may benefit from soft magnetic composite (SMC) or sintered soft magnetic (SSM) materials, material processes exclusive to powder metallurgy. How do SMCs compete with lamination steels? Let’s take a look.
Spoiler: It’s only with powder-based electric motor core materials that you can reduce a product from 1,300 to 5.
Magnetic Powder vs. Laminates for Electric Motor Efficiency: Basic FYIs
Electromagnetic motor design typically involves one of three material processes. Two from the world of powder metallurgy (PM), and one using laminate (typically formed via stamping).
Soft magnetic composites are ferromagnetic powder particles ideally coated with a uniform layer of electrical insulating film. SMCs are ideal for AC electric motor design. Parts formed from SMCs are compressed just like any traditional powder metal part, but undergo a "less-hot" heat treatment process than ...
... Sintered soft magnetic materials, which are -- you guessed it -- sintered. Like SMCs, they are powder-based and additive in nature. Unlike SMCs, advanced manufacturers can heat SSM materials up to 2500 °F to better balance magnetic and strength properties. Sintered powders are ideal as a DC motor magnet material.
Steel laminates, however, are NOT formed by a powder metal process. They instead come from a solid block of raw steel that the manufacturer stamps or into strips. Think of your bathroom or stovetop exhaust fan as an example. That motor has 6-7 laminations stacked in there. Each one is a little thinner to compensate for a laminate’s inability to form a rounded shape.
(DYK? Heat = thickness squared is a good rule of thumb. A component 2x as thick as another component will generate 4x the heat. But with powdered metal, we throw those rules out the window. We take each particle and make a mini-lamination in the assembly.)
Limitations of Motor Lamination Material
Lamination steels have been around since the invention of electricity. Yet they have limitations factors affecting the efficiency of electric motors.
Think about a piece of sheet steel that's rolled thin and stamped. You’re limited to a 2-D shape. You can stack sheets to get a 3-D effect, but it’s still not true 3-D.
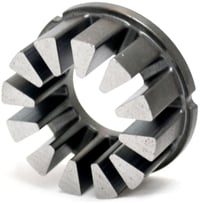
Example: Say you need 100 laminations in your rounded part design. You have to make each one a little less wide than the previous. (Think of a toddler’s toy ring set.) This tends to make the electric motor assembly process complicated. Shuffling laminations together to make the right shape can be a huge pain.
Another example: Look at this design. How would you be able to do that in lamination? There’s simply no way of holding it together easily. The complexity involved in making that shape is very high.
Soft Magnetics Thrive in High-Efficiency Electric Motor Design
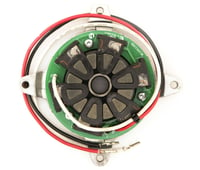
A soft magnetic composite is not just a series of thin sheets. Instead it’s something that can become a truly unique shape.
Creating a round component is easy with powdered metal. In fact, you can achieve it with a single press stroke!
The design stage becomes much more efficient with SMCs in a case like the part above. You have that shape on the outside and a step-down region on the inside, followed by another tall shape on the inside. That’s almost impossible to do with lamination. It can be done with powder metal.
Why are rounded corners such a big deal? SMCs’ ability to form these allow you to reduce
- Copper cost
- Copper loss
- Motor winding material
- End windings
You can wrap a copper wire around these parts quite nicely -- no air gaps! Air gaps don’t contribute to magnetic performance, so SMCs get rid of them.
Soft magnetics allow engineers designing a motor or transformer to put metal where it’d be beneficial for the circuit.
What about space and weight? By requiring less material and facilitating a more rounded design, soft magnetics can give you a more compact final assembly. In, say, an electric vehicle or a drone, you could reduce the vehicle's weight or free up room to add other features.
Secondary Advantages of Shape-Making With the Powder Metallurgy Process
There are several ways to assemble laminated parts. Each has something it does well, but none of them compare to the possibilities of a soft magnetic powder assembly.
Beyond what we already covered at length, they include:
- 95%+ material use -- because you start a powder metal part from scratch, there's minimal scrap waste.
- Expanded motor design options -- powder metal frees you to consider higher-performing alternatives like axial and transverse flux motors.
- Reduced core losses -- Hysteresis and eddy current losses increase the heat in a magnetic material. And heat = an inefficient electric motor.
- High-frequency applications -- Once you start stacking them, laminations fall behind SMCs at as low as 60 Hz. Even an SMC part of similar length to a lamination stack will produce similar performance as a much smaller SMC part. Powder metal is an option up to 10,000 Hz ... and possibly beyond!
Depending on the application, a soft magnetic part made from PM may also outperform similar parts made via machining, casting, and forging!
Possible Limitations of Powder Metal Soft Magnetics
A soft magnetic composite won’t work for every motor application. These thin, small parts do have a few caveats:
- Low strength of final material (with SMCs) -- there will be limited applications for a rotating component. By instead choosing an SSM material, you can greatly improve strength while still achieving competitive magnetic properties.
- Less permeable than lamination -- permeability will be density-dependent, and you need greater current to achieve the same level of magnetic induction. Note that the linear response of an iron powder might actually be advantageous in some parts.
- Lower magnetic saturation than lamination.
- Slower press run -- this doesn’t necessarily mean powder metal is less time-efficient than lamination. Yes, lamination presses run at 100s of strokes a minute, but if you need numerous laminations to make an assembly, the single-press stroke powder metal process may still be quicker.
More Tips for Optimizing Electric Motor Efficiency
By far the biggest factor that separates soft magnetic powder from motor stamping material is the former’s 3-D shape-making capability.
An electric motor's stator or rotor design will use fewer and more easily manufacturable parts, taking your cost and space efficiency to the next level.
You can even combine soft magnetic composite with a laminate or sintered part to achieve the most efficient electric motor design possible. By thinking differently and not accepting the same-old, design possibilities open up exponentially.
If you need more help advancing your electric motor or other electromagnetic design, consult our Soft Magnetics Resource Hub:
(Editor's note: This article was originally published in May 2018 and was recently updated.)