“Reduce” is certainly a popular word among high-efficiency electric motor designers. They want to reduce costs, of course, but also reduce core loss and assembly size where possible.
So where is “possible?”
One of the common complaints of axial motor engineers using traditional steel lamination options is the cumbersome nature of working around the limitations of stacking numerous pieces for a single finished component. This is a shared headache among the three lamination assembly options we compare in the infographic below. However, we’ll also compare a non-lamination alternative -- soft magnetic composite material -- whose claim to fame is reducing the number of components in an AC stator or rotor design.
Let’s review a visual side-by-side of these electric motor assembly processes:
Electric Motor Assembly Process Chart -- Axial Flux Motor Design
Here are the processing steps, advantages, and disadvantages for:
- Coiled steel assembly
- Standard steel sheet assembly
- Steel sheet assembly with vertical laminations for poles
- Powder metal -- soft magnetic composites
The finished images above may be how you dream your part will come together. However, there's a misconception to the cost and ease of manufacturing an electric motor.
Option A: Mandrel-Wrap Long Strips of Sheet Steel
This process, typical in axial flux motor design, involves wrapping the magnetic material around a mandrel, welding it, and machining out the pole pieces. Annealing may be necessary afterward to reduce core loss and improve magnetic performance.
While the process isn’t too difficult from start to finish, it does lack polish. The top issues are:
- Material inefficiency -- up to 50% scrap waste
- Shorting between wrapped layers
- High core losses, reducing the motor’s efficiency

Option B: Radially Stacked Lamination Steel
This process starts with flat, laminated electric steel sheets. The manufacturer stamps out the necessary shapes, sorts them, and assembles them in a radial orientation. Again, annealing may be necessary to maintain magnetic performance.
This method of using steel lamination is kinder to your wallet from a material-use standpoint. Unfortunately, it’s inefficient in other ways:
- Sorting and assembling is cumbersome
- Gluing, welding, and staking subcomponents can reduce magnetic performance
- Least-desirable magnetic flux orientation
This assembly method is quite common in radial flux motor design, and certainly sufficient when high performance isn’t necessary. If you need more efficiency at higher frequencies, keep moving to the right on the chart.
Option C: Vertically Stacked Lamination Steel
Now we’re getting somewhere.
This electric motor assembly process is much like the last, except it uses vertical laminations for poles.
As before, the manufacturer stamps laminations of varying sizes, then assembles them via welding or another joining process. There’s an added step of machining the inner and outer diameters, and possibly annealing.
Like the radially stacked option above, this vertical option more efficiently uses the material compared to coiled assembly. Unlike radial stacking, vertical stacking allows for proper orientation of poles for magnetic flux carrying while maintaining operational efficiency.
Where does it still fall short of the ideal solution?
- High cost to assemble
- Potentially labor-intensive
- Core losses still an issue
Option D: Soft Magnetic Composite Powder
Finally, we come to soft magnetic composites (SMCs). This family of electric motor core materials consists of powder particles coated with an electrically insulating film.
Unlike laminations, powder metals (like SMCs) create parts through an additive process, rather than subtractive. The powder metallurgy manufacturer compacts only the material needed to form the final part, then heat treats it and handles any assembly necessary.
The many advantages of advanced powder metallurgy help SMCs outperform laminations in AC electric motor design:
- Optimized magnetic flux path -- lamination sheet orientation isn’t a factor, so the flux flows wherever you want
- More reliable core loss reduction -- air gaps formed during laminating drastically reduce permeability as you tack on additional sheets
- Useful at frequencies up to and exceeding 2,000 Hz
- 95%+ material efficiency
- Net-shaping capability for complex, unique geometries
- Longer parts don’t degrade performance
That last point may have raised an eyebrow. Some engineers assume powder metallurgy isn’t an option for their project because of part-size limitations. Actually, through segmentation, SMC parts can facilitate easier winding, reducing core losses even further.
Since there’s rarely a perfect solution in manufacturing, we should know there’s one drawback to SMCs: reduced strength. SMCs can’t be sintered to improve strength, as the extreme heat would make the final component excessively lossy.
Consider your application’s end use and whether the many benefits above outweigh the modest reduction in strength.
Electric Motor Materials’ Role Today (& Tomorrow)
As the efficiency of “electrification” continues to develop, electric motor materials can be the key to that magic word of “reduce.”
Reducing your assembly steps, and reducing the core losses and wasted resources inherent to the lamination process, is achievable with today’s powder metallurgy. With SMCs in your AC motor assembly, “possible” is easily within reach.
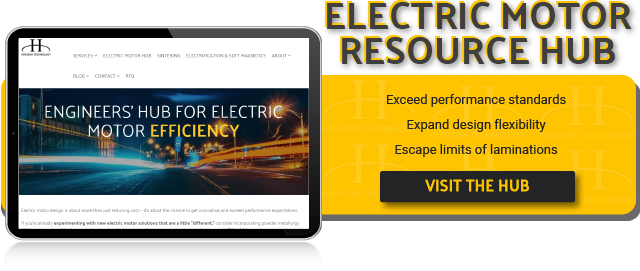