When designers think of powder metallurgy (PM), they often visualize small gears, clutch plates, porous filters, and many low strength structural applications. Advances in processing and materials enable PM to compete in high strength applications such as connecting rods, main bearing caps, planetary carriers, etc.
An often-overlooked potential for PM is in the area of DC magnetic applications. The inherent advantages of PM such as customizable performance, unique shape making, minimal waste promoting sustainable manufacturing can all be applied to your magnetic devices. This interplay between design freedom coupled with PM technology and manufacturability creates a perfect storm - allowing engineers to fully realize the potential of electrical applications through powder metallurgy.
A bit of history, PM sintered soft magnetic (SSM) applications burst into prominence about 50 years ago with the Delco 5MT starter motor and exhaust gas recirculating valves. These early groundbreaking applications, led to further enhancements in materials and processing giving a broad spectrum of materials, magnetic performance, and structural performance to meet a wide variety of applications. Let’s take a closer look at sintered soft magnetic (SSM) materials and explore the potential for your applications.
Sintered Soft Magnetic (SSM) Materials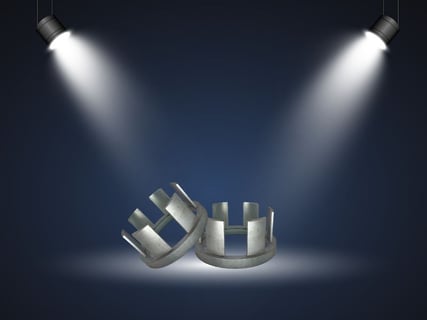
PM utilizes a wide range of materials, including:
- Pure iron
- Alloys of iron and phosphorus
- Alloys of iron and silicon
- Alloys of iron and nickel
- Ferritic stainless steels
All of which can be tailored for specific applications.
For example, using different metal powders with specific properties can create unique magnetic characteristics, coupled with high strength, corrosion resistance, or wear resistance.
Critical magnetic performance can be classified in terms of the following magnetic properties:
Permeability: How quickly a component can be magnetized. High permeability requires less current to magnetize the part - delivering a faster response for applications such as solenoids or relays.
Saturation: Is defined by the electromotive force created by the applied current through the windings. Two key characteristics are:
- Maximum saturation flux density (Bsat) of a PM component is the maximum magnetic energy that can be stored in a part - a linear function of the relative density.
- Induced magnetic flux below Bsat is influenced by the density, material, and processing.
The figure below shows how Bsat is affected by density and compares this to other materials.
Coercivity: Is related to how much reversed current is required to take the component back to a state of zero magnetism. Often a key in applications such as relays and solenoids where opening or closing is a critical performance function.
Thermal Stability | Corrosion Resistance: If corrosion resistance and thermal stability is required, then PM ferritic stainless steels can be specified. Early anti-lock brake systems used stainless steel sensor rings to control the anti-slip feature. Subsequently, a less costly iron/phosphorus material combined with a surface treatment provides the same level of corrosion protection.
Magnetic Materials – Processing
Impacts on Performance
The above figure is a representation of the magnetic performance of PM materials and processing. At the low end of the magnetic performance, you have pure iron and iron phosphorus materials conventionally compacted and sintered at 1120 °C (2050 ’F) to densities up to about 7.1 g/cm³.
Pure iron is the logical starting point for many designs as it offers permeabilities up to about 2500 with a coercivity of about 2.0 Oersteds and is the lowest cost alternative. This combination of magnetic properties is useful in motor applications which simply require back iron as the magnetic flux path and certain speed sensor applications.
Iron phosphorus materials are the next step in magnetic performance and cost - conventionally compacted and conventionally sintered. This material system can give permeabilities up to about 3200 with a coercive force of around 1.5 Oersteds. Iron Phos materials have an additional advantage – 2 times the tensile strength of iron.
Both the pure iron and iron phosphorus materials conventionally process can be classified as a good design approach for many applications.
However, what if your design requires higher perm and saturation? A logical transition is to the iron phosphorus material now with the benefit of advanced compaction technologies. The higher densities - up to 7.3 g/cm³ will promote higher perm - up to 4000 coupled with higher saturation induction.
This is a slightly more expensive alternative and represents a better approach to higher performing product design.
What if your design requires still a higher perm and higher saturation? Two options present themselves - one is the iron phosphorus material coupled with advanced compaction technology coupled with sintering at 1260 °C or 2300 °F or an iron silicon material sintered at 1260 °C or 2300 °F. These two material and processing options can produce permeabilities approaching 5000 with coercive values of about 1 Oersted.
Comparing these results to those previously discussed, they represent the best approach for magnetic performance.
If the best approach is still not good enough, does that eliminate sintered soft magnetic components? The answer is NO! Recently, Horizon Technology developed an iron silicon material with permeability values reaching nearly 7000 and with coercive force values of about 0.7 Oersted. This processing takes the best of advanced compaction and couples it with Ultra High Temperature Sintering 1370 °C or 2500 °F, enabling ultimate DC magnetic performance unsurpassed in the PM industry.
Applications for PM Sintered Soft Magnetic (SSM)
Almost any DC magnetic application can benefit from PM’s unique shape making, material efficiency, and customizable magnetic and structural properties. Applications such as:
|
|
|
|
|
|
|
|
|
|
Although the trend in the automotive industry is away from IC engines and toward electrification, many of these tried-and-true DC designs will live on with perhaps higher performance demands. PM can meet these demands and offer a sustainable technology approach to your component design.
Call or visit the Horizon Technology web site to get more information about sintered soft magnetic materials. We can provide magnetic data suitable for use in magnetic modelling programs to verify the applicability of your design concept.