Manufacturers are always looking for an advantage. Often they’re comparing apples to apples, but when they really crave innovation or a more cost-effective part, they look outside the box.
What you think you know about powder metallurgy may not be true anymore. Powder metallurgy is being looked at more than ever as a replacement or complement for competing metal forming processes.
Three of the most logical competitors for powder metallurgy are:
- Machining
- Casting
- Stamping
The rules of powder metallurgy have changed in the last several years. Does your metal forming process of choice still stack up to the modern advantages of powder metallurgy? Keep reading! (Or download the expanded PDF version below.)
Advantages of Powder Metallurgy Vs. Casting, Machining, & Stamping
The following table presents our opinion of how powder metallurgy ranks relative to other manufacturing alternatives in every attribute that matters to the customer. In this exercise, 10 is regarded as perfection and 1 is the absolute worst.
(Note that we’re using “powder metallurgy” in the conventional sense and leaving metal injection molding and additive manufacturing, aka 3D printing, out of it for now. You can compare those processes to conventional powder metallurgy by downloading the full, free e-book version of this blog post -- just click the graphic.)
Process Capabilities
Process capabilities refers to the expected variation of a process
Machining and stamping leads the way because both are manufactured without thermal processes to produce a final shape. Because you either machine or stamp to a net shape, precision is going to be inherently higher.
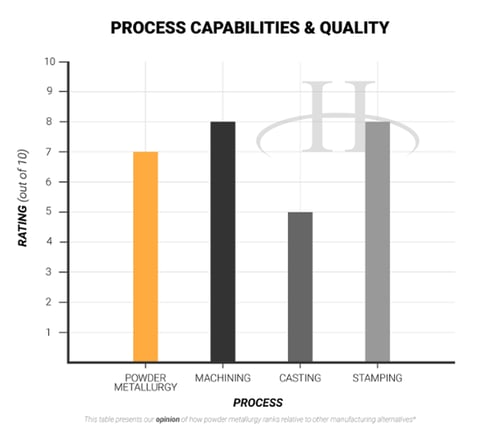
As you probably know, powder metallurgy (PM) and casting undergo a thermal process during production. In powder metallurgy it’s sintering -- a wonderful tool to have, but it comes with certain distortions. Dimensionally, the “green” part you get from powder metallurgy is every bit as good as machining and stamping; it’s the sintering that’s a bugaboo.
Greater design tolerances are required with casting because of the very nature of the process. Powder metallurgy’s precision dies, punches, and core rods produce net shape components with closer tolerances than die cast parts. There’s always the option to use a variety of secondary operations on your cast or powder metal part if you need further refining.
Nevertheless, powder metal is clearly more consistent. A uniform weight of powder is deposited into the die, then compacted to the same density. Unless your powder metal manufacturer has poor housekeeping practices, contamination and defects are rare.
The Control Factor
Another advantage of powder metal is microstructural control through cooling. In casting this depends on cooling rate, which varies based on surface area and volume. The composition is the same throughout the part, but because of the different cooling rates, the microstructure and resulting properties can vary.
With PM, these are factors we try to control to minimize differences from batch to batch. Powder metallurgy provides much greater control and consistency.
Why does this matter to the designer? Powder metallurgy can produce harder, tougher components than casting can. And you can have a wider choice of alloying and raw materials to work with, unlocking the use of PM in more demanding applications.
When it comes to machining, quality will be somewhat dependent on the level of technology you’re using. CNC quality is nearly unmatched; manual machining not so much. Advanced software available for CNC machining helps you easily match specifications of complex parts, with little room for human error.
Stamping is a long-established process used in a variety of applications. Realistically, if the part can be made via stamping, that's likely your best option. However, stamping lacks the 3D capability and alloy flexibility of PM and can often leave tool marks and scratches on the products. Still, it can give you reasonably well-performing parts. The thickness of the workpiece and choice of raw materials often limits stamping. It’s rare to stamp something much thicker than 0.25”, and the material is often low-carbon steel.
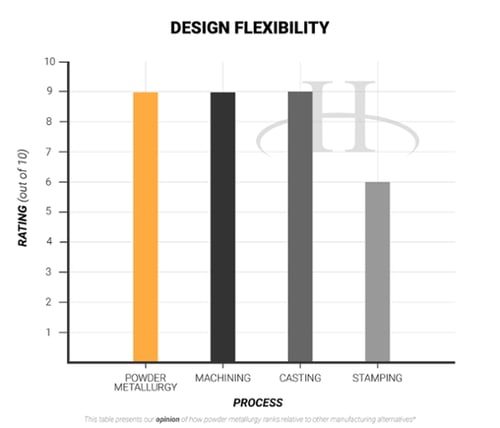
Design Flexibility
Powder metallurgy and casting have the unique ability to turn nothing into something -- that is, it’s additive rather than subtractive. Characteristics of powder metallurgy include the ability to control porosity and durability with just the right mix of materials. Note that casting can produce larger parts than possible with powder metallurgy. Can we also mention the ability to use either sinter brazing or sinter bonding to make even more complex shapes; this is a poor man’s way of getting more 3D like metal injection molding or additive manufacturing.
Powder metallurgy’s and casting’s “from scratch” nature also allows for 3D designs -- with virtually no cost added -- that are impractical or impossible otherwise, especially in stamping.
The tricky aspect of metal stamping is that there’s barely any flexibility in the shape and thickness of the sheet metal. Complex parts will require additional steps to production, jacking up your cost.
Affordability per Part
Product cost-effectiveness is by far the predominant reason for choosing powder metallurgy and is the main driver of the structural parts industry. PM wins the cost competition vs. other processes on the basis of:
- Elimination of process steps
- Lower energy consumption
- More efficient material use (more on that below)
- Design flexibility and ability to make complex shapes
Stamping gets a slightly higher rating on the chart, but you’re limited by size and shape.
A caveat: Much of this depends on project volume. It’s rarely going to be cost-efficient to make 10 powder metal stators for your next electric engine design.
If it’s feasible to make your component with the stamping process, then stamping is a very logical, economical choice. Again, as a stamped component gets more complex, the price will rise.
Machining is well suited to low-volume, highly complex parts.
Material Strength
With machining, you can take any kind of steel you want and slice and dice it. Machine shops work with some really high-strength materials that give great performance.
Powdered metal parts, because they have holes, won’t necesssarily have the same level of strength as a machined part. If you need to pick between powder metal and casting, though, stick with PM:
- Better wear resistance
- Higher operating temperatures
- Can use corrosion-resistant copper and stainless steel
Casting offers a wide range of properties and performance requirements. Powder metal, however, is capable of meeting each of those requirements. Choosing between the two depends on your desired part size, shape, and other design considerations.
Stamping is typically limited to relatively low-strength materials because of its very nature. High-strength materials tend to break the tools. Therefore, most metal stamping materials are low-carbon iron or steel.
Scrap Efficiency
Powder metal and cast parts eliminate the waste found in stamping and machining when creating components with holes or varying thickness. You can once again thank the batter-like material that allows you to use only what you need.
Take stamping as a troublesome example. Since the raw sheet material comes in uniform width and thickness, it may not conform to the requirements of the blank. Stamping also requires material to clamp the sheet metal in the die. That’s a double whammy of waste.
Recycling is an option, but scrap from machining and stamping only recoups a fraction of the raw material cost.
Tooling Affordability
One perk of CNC machining is that it’s better for low-volume parts -- no tooling cost is required.
Powder metallurgy’s cost effectiveness generally hinges on large production quantities. If the volumes are too low, you can’t amortize the costs of your long-lasting tooling or mitigate the time lost to frequent tool changeovers.
Luckily, you can reduce tooling costs for powder metallurgy by following some simple do’s and don’t’s.
Many feel that casting tooling is the biggest drawback of the process because of its high cost. On a similar note, stamping is not ideal for low-volume projects in part because of the enormous cost of tooling.
Machining definitely wins this battle hands-down.
Lead Time
You should judge your contractor’s delivery from the start of an initial order to delivery of the first part.
Powder metallurgy has always been a high-volume part-producing technique. So if you need a limited number of components, the per-part speed of delivery may disappoint you. It may take the powder metallurgy company almost a month to get the powder in-house. You can tack on a few weeks of production after that.
A machined part only takes a few weeks total. You put a piece of bar stock in the CNC mill, and you start whittling away.
But once you have a tool in place, that's when powder metallurgy suppliers begin to shine. Yes, you can machine 5-10 components a lot faster -- but if you want 10,000 of them, powder metal is an ideal scenario.
If you need to produce high volumes with any level of complexity, casting is usually a stronger choice than stamping. Because metal stamping dies can produce strong parts quickly, some may opt for stamping if they have a big order and a tight deadline.
Additional Comparisons -- Forging & More
Grab this free download to learn more about powder metallurgy vs. stamping, casting, and machining. We also compare:
- Powder metallurgy vs. additive manufacturing (3D printing)
- Powder metallurgy vs. forging
- Powder metallurgy vs. metal injection molding (MIM)
- Powder metal materials vs. steel lamination (electrical steel)
You may discover your product is missing out on cost and performance benefits you never knew existed!