We have well established the benefits of using SMC materials in stator applications compared to lamination steels. SMC powder metal can improve performance and reduce the manufacturing and operating cost of a motor.
Engineers working on larger motors may feel they are not able to take advantage of the SMCs due to the limited size of parts powder metal can produce.
In most traditional metal applications this assumption would be correct but in the world of SMCs there is a novel solution to size and even shape. That solution is, segmentation. But what exactly do we mean by segmentation?
What is Segmentation?
Think of segmenting as breaking down a very large part into smaller manufacturable parts then assembling them to form a larger, complete assembly. Segmenting can provide a tool for engineers to skirt the problem of size constraints.
So, segmentation solves the “no press large enough” problem, but how can it actually improve BLDC motor design?
A section of a stator coil
Why Use Segmentation for BLDC Motor Design?
Before we get into the nitty-gritty details of improved brushless electric motor design, it’s important to talk about why engineers consider segmentation in the first place. There are three primary reasons why you’d need (or want) segmentation:
- Part is too large to produce traditionally
- A unique shape which cannot be molded in traditional pressing technology
- Reduced core losses and lower costs
Manufacturing Large Powder Metal Parts
As we mentioned, traditional powder metallurgy (PM) is limited by the size of the components it can create. The limits of size are driven by the size of the press the part will be molded. In powder metal pressing or compaction the size of the press is expressed in tons.
A press can be referred to as a 500 ton press. This is a reference to the maximum force exerted by the press which has a direct correlation to the size of part that can be compacted.
Let's break that down.
Pressing a typical soft magnetic composite to a 7.4 g/cc density you will require about 600 megapascals (MPa) or 45 tons per square inch (TSI) of compaction pressure. But that’s only half the story, now we need to calculate the planar surface area of the part you want to produce and multiply it by that compaction pressure. So, a part with a projected surface area of about 11 sq. in. pressed to 45 TSI to achieve a 7.4 g/cc density will require about a 500-ton press.
As presses get larger they also become less available to source your product. A sweet spot of press availability by size might look like this:
- 500 tons can produce a part of about 11 SIPSA. These presses are readily available in the industry
- 850 ton presses can produce parts up to about 17 SIPSA. These presses are about the limit of availability
- And presses above 850 tons become rare and are typically program specific requiring enough volume to consume a significant portion of its available capacity
As with many things, larger parts bring more challenges that must be accounted for within the tool design and manufacturing manufacturing process to ensure the integrity of the part is not compromised. Remember, your SMC part is not sintered, so handling and especially shipping must be considered in the design stages.
The Benefits of Assembly
Say your PM manufacturer has large presses in-house and size isn’t an issue. Why would you want to use segmentation over a single press-and-sinter part?
It comes down to your application. For brushless DC motor design, having segmented parts might actually improve the assembly process.
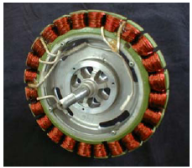
A motor assembly made with segmented stator coils
Motor stator design can be broken into two different kinds of parts: the round base, and the individual coils. The coils need to be wound with copper wire, and if they’re separate rather than joined to the base, winding is easier.
“But how do you join the parts back together?” you might be thinking. Well, many segmented parts are designed with interlocking features to ensure they’re aligned correctly when assembled. The epoxies used to glue the parts together equal the strength of the actual powder metal material.
The more segments, the greater the impact on magnetic performance, however that can be offset by certain blended epoxies, which we're continuing to research.
Plus, depending on your part and the processes used, segmented assemblies have the potential for cost savings compared to other methods of large part manufacturing.
Pros | Cons |
Take advantage of SMC materials for large parts | Potential impact on magnetic performance |
Copper wire winding is easier for segmented stators (reduced assembly time/cost) | More tolerance may be required as opposed to pressing a single part |
Opportunity to reduce cost of the component | Not enough customers are using this great process yet! |
Advanced shape-making to enhance the magnetic flux path |
How Can Segmentation Improve BLDC Motor Design?
When thinking about improving a single press component for an electric motor design, we often turn to soft magnetic composite materials to improve magnetic properties and strength. What if we combined the benefits of SMCs with the benefits of segmentation for BLDC motor design?
SMC provides the opportunity to increase performance and decrease cost of your component SMC parts are generally more energy-efficient parts.
Now think about segmented parts. Segmented parts can make hard-to-wind stator coils easier, faster, and less stressful for the engineer. But, it also allows for more accurate windings, which have the potential to reduce core losses.
That’s right -- reduce core losses.
What will happen when you combine an energy-efficient SMC material with the potential for more accurate windings? Because of...
- Smaller component sizes
- Decrease energy consumption
- More efficient windings
… engineers should be able to significantly reduce core losses in electric motors. This will decrease overheating and excessive energy consumption in electric vehicles.
The dimensions of a segmented stator
Segmented PM Parts for Better BLDC Motors
Even if your electric motor components aren’t large enough that segmentation is your only option, you should consider the assembly benefits of segmented parts.
If you need to meet specific levels of magnetic performance, a single-piece SMC component might work best. However, as engineers continue to explore the possibilities of reduced core losses and improved magnetic performance with segmented PM parts, it’s worth considering segmentation for building better BLDC motors.
To learn more about how the PM world intersects with the electric motor world, visit our new Engineers’ Hub for Electric Motor Design.