Why are magnetic materials important? Without magnetics, modern technology wouldn’t exist. They’re in motors, transformers, cars, and so on. And powder metallurgy materials are often the best way to deliver the key magnetic properties that literally drive these applications.
Consider the following charts and information a nice, little handbook of advanced magnetic materials and their properties. Specifically, we'll discuss both sintered soft magnetic materials (SSMs) as well as soft magnetic composites (SMCs). Even competing materials will be introduced!
Why Do Powder Metallurgy Materials Need to Be Magnetic?
Glad you asked. Engineers use magnetism to convert electrical energy to mechanical energy. Some of the most obvious examples are:
- Electromagnetic generator design
- Alternators
- Hydropower
- Transformer core material selection (to supply constant voltage)
Advanced Powder Metallurgy Magnetic Materials:
Ferromagnetic materials (ones that are magnetic and contain iron) are great for those seeking advanced powder metal parts. They include:
- Iron
- Nickel
- Cobalt
- Alloys of these materials
They can also be ferrites or iron oxide compounds. For more detailed information on different metals used in powder metallurgy, scroll below.
The high permeability of ferromagnetic materials is a key characteristic. This quality is great for applications in which you need lightning-fast response to an applied current.
About the Magnetic Performance of Your Powder Metal Parts
Magnetic performance is a function of:
- Alloy system used
- Density of final part
- Saturation induction and magnetic permeability, which are influenced by density
- Sintering temperature
- Carbon and nitrogen contents after sintering
Ferrous Sintered Magnetic Materials in Powder Metal -- Density & More
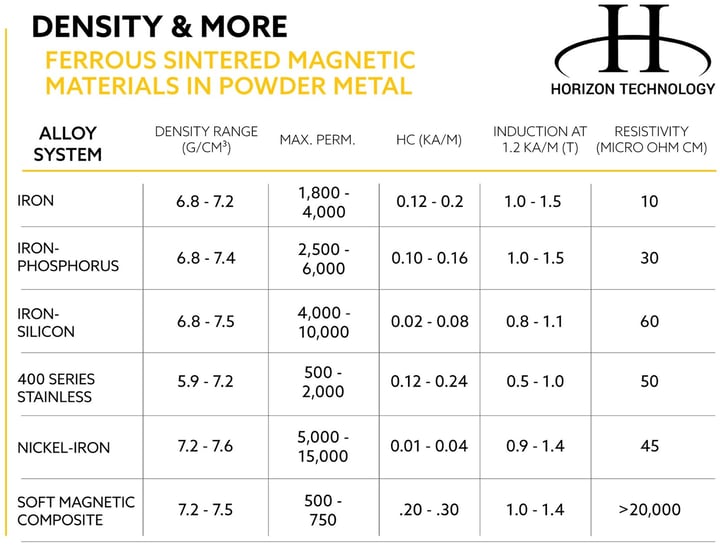
The chart above gives you a good idea what to expect with powder metal material properties. “Induction” refers to magnetic induction, aka magnetic flux or flux density. These terms refer to the process in which a material is magnetized by an external magnetic field.
(Related article: Full flow chart of material possibilities, including for structural parts)
Property Comparison
Sometimes you need some strength to complement the magnetic properties of your device. The table below shows a comparison of two powder metal alternatives to a common steel used in electrical applications.
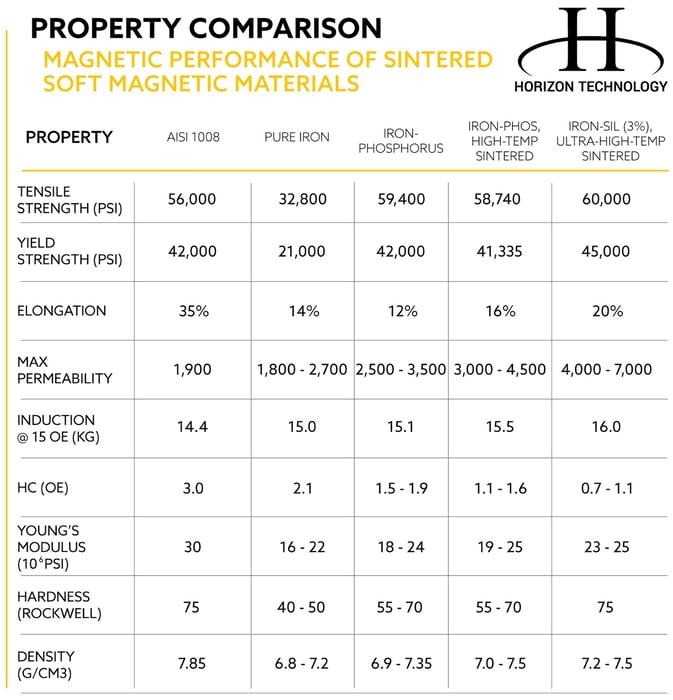
AISI 1008 is a common carbon steel. Iron-phosphorus (FY-4500) is a grade of powder metal that contains 0.45% phosphorous.
Think of pure iron as your base material for DC applications. The FY-4500 is more advanced, though still less advanced than, say, a 3% silicon material. These two are also geared toward DC applications.
Whatever your magnetic application, the name of the game is good magnetic performance that still balances mechanical performance.
More on Metal Types
Stainless Steel
Stainless steels used in powder metallurgy are mainly ferritic grades mainly used in corrosive environments.
Martensitic stainless grades 409L and 434L are widely used in magnetic sensor applications where corrosion resistance is important.
Stainless steel generally has lower induction than iron or iron-phosphorus systems.
Iron-Nickel Materials
Iron-nickel pre-alloys are 50% nickel and 50% iron. Expect high-magnetic-permeability materials and a rapid motion with low coercive force -- think of the old dot matrix printers.
Low induction and low applied magnetic fields are the trademarks of iron-nickel.
Because of the high nickel content of this alloy, the cost is high.
Iron-Phosphorus
Iron-phosphorus materials feature high induction, strength, and hardness. Its resistivity is merely so-so.
It’s notable that this alloy’s ductility allows for riveting operations.
Applications for this metal include:
- Electric stator core and rotor material for low-speed stepper motors
- Electric starter motors and pole caps
- Actuators for valve control
Iron-Silicon
Iron-silicon sintered parts respond better than iron-phosphorus sintered parts at moderate frequencies. This powder material is used in actuators where impact is involved, such as impact printer heads.
Soft Magnetic Vs. Hard Magnetic Material
Soft magnetic materials can be easily magnetized and demagnetized. Examples include:
- Iron
- Nickel-iron
- Lamination steel
“Soft” in this case refers solely to the magnetism and has nothing to do with the material’s strength or hardness.
Hard magnetic materials, as you probably guessed, are very difficult to magnetize and demagnetize. Examples include:
- Ferrites
- Iron-neodymium-boron
- Samarium–cobalt
Hard magnetics see popular use as electric motor core materials.
Wait, What Is a Soft Magnetic Composite?
A soft magnetic composite (SMC) is an iron-based powder coated with an insulating layer that can be used in AC electrical applications. A non-sintered material, SMCs' electrically insulating boundaries offer unique magnetic performance:
- High magnetic flux density
- High torque
- Reduced core loss
Most published data evaluates the core losses of lamination steel based on a single sheet. But what happens when you stack them? SMCs start to outperform them at as low as 60 Hz, as you see above.
Note how these parts outperform electrical steel lamination assemblies, even at larger heights:
One of the unique attributes of SMCs is that you can match a grade to your desired frequency range. Since these are advanced, custom materials, consult with Horizon for the nitty-gritty details.
B-H Curves of Soft Magnetic Composite Vs. Lamination
This B-H curve chart shows the performance of soft magnetic composite versus a frequent competitor, laminations. The chart shows the relationship between magnetic flux density (B) and magnetic field strength (H) for a particular material.
Induction of soft magnetic composites is a function of density. Saturation induction of composites is a function of density according to the following equation:
Bs = 2.2 x density (g/cm³) / 7.85
Bs is measured in Tesla.
These are key values that engineers and purchasers should look at when choosing magnetic materials. It’s all about the magnetic response as you apply a field and remove a field. It’s truly helpful stuff for purchasers looking to get on the same page as their parts supplier. And if it’s all too confusing, just ask for help!
Disclaimer: Soft magnetic composites, while generally amazing, are not sintered. As such, they are brittle and are not recommended for rotating components. We’ve exhaustively covered all the good stuff soft magnetic composites can do here.
Need More Information? Expertise? Confusing Charts?
We have many more charts and resources that get into the complexities of both sintered and SMC materials:
- Mechanical properties
- Magnetic properties
- Much more
Check out the Engineers' Hub for Electric Motor Efficiency:
(This article was originally published in October 2018 and was recently updated.)