Famous automakers around the world rely on the sintering process in powder metallurgy to improve their components’ performance and economic efficiency. New advances in sintering can lead to even higher overall performance for those automakers -- as well as other industries.
But the advantages of sintering are a moot point if your manufacturer can’t control the process.
Sintering furnace problems can ruin the metallurgy, shape, magnetic quality, and other properties of your component. To meet the exacting demands of automakers and other industries, many metallurgical companies have installed automated systems to continuously monitor the furnace’s most important operating parameters.
For sintering or sinter hardening -- a strength-enhancing technique only available in PM -- that means adding real-time analysis. At Horizon, our furnace’s specially designed “S.M.A.R.T. System” informs us immediately of changes in the furnace that could impact your final product.
Keep reading to learn how we’re raising powder metallurgy sintering and sinter hardening standards to meet the demands of IoT and Industry 4.0.
Why the Need to Control Sintering?
Your powder metallurgy supplier should work hard toward reducing spills, recalls, and warranty claims related to sintered components. Horizon’s new S.M.A.R.T. System -- the work of Abbott Furnace -- emphasizes continual monitoring, defect prevention, and reduction of variation and waste in the supply chain.
The new system helps meet customer expectations, along with many standards of the auto industry and elsewhere. One example is the CQI-9 “certification” some automakers require of parts suppliers for heat treating management and continuous improvement. CQI-9 is not something powder metallurgy manufacturers get “certified” to, no third-party auditor is knocking on our factory door, and it only affects a small sector of auto parts makers. But it has been a great catalyst for a push toward continuous improvement of the sintering process.
Here’s how our advanced sintering furnace helps us collect valuable data for the customer’s peace of mind:
The Advantages of Sintering S.M.A.R.T.er, not Harder
Controlling sintering parameters means understanding the four primary variables of sintering:
- Temperature: More heat will give you more strength and ductility. About 80% of the powder metal industry can reach sintering temperatures of 2050° F. Some furnaces reach temperatures up to about 2300° F. Horizon’s can reach 2500° F. When the powder metal part goes through the production part approval process, it’s imperative that the process is controlled to produce parts exactly like the first articles. Thus, the importance of consistent sintering temperature from lot to lot is imperative. The key here, however, is to manage the temperature within a specific range to control the metallurgy part.
- Time: This is a tricky variable, since more time at peak temperature improves sintering, but longer time may contribute to the microstructure getting roughed up rather quickly. With longer times you may also run into dimensional control issues that will shrink the part beyond its specifications. Again, once the proper metallurgy is determined, the key is to control the time within a specific range.
- Atmosphere: One common theme here is keeping the threat of oxidation away. Other controlled conditions grant benefits such as improved magnetic performance and higher strength. Your manufacturer can adjust the atmosphere based on your priorities. In all of these the key is to know there is a problem as soon as something changes in the furnace and not wait to detect a change after it exits the furnace.
- Cooling: This is critical for sinter hardened parts where a minimum hardness and martensite content is required after the sintering/cooling steps.
Historically, tracking furnace performance has been a manual process. With Horizon’s new continuous improvement add-ons, we can monitor the tolerances we’ve established on these three variables in real time. The technology allows the manufacturer to establish specification ranges in the controller itself.
There are electronic outputs coming from:
- All temperature-controlled zones
- The belt speed
- The main atmosphere flow sensors, plus the dew point and oxygen sensors
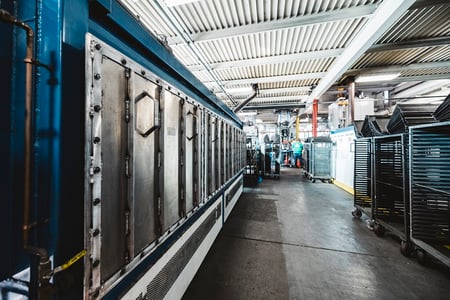
The most important role our new system plays is checking the chemistry of the atmosphere. In the past, your supplier’s engineers would have to wait until the component exited the furnace to see how it turned out. Now the engineers can be notified of changes immediately.
Typical powder metallurgy companies have control over these variables to some extent. But all they get when a problem arises is an audible alarm. Horizon’s setup includes an audible alarm, but we also receive continuous data so we have historical reference for the furnace’s performance.
Customer Benefits of Highly Controlled Sintering
The new furnace technology isn’t just a simple failure analysis of heat-treated steel components. It’s about capturing the furnace’s performance in good times and bad. This peek into associated product quality for any day and time means there’s no veil over transparency.
The customer gets the benefits of:
- Limiting the risk of a defective batch. Your manufacturer can take immediate corrective action regarding the furnace’s atmosphere. In the past, the manufacturer would have had to wait for defective parts to come out.
Actual evidence and assurances when your supplier says, “Here's how that happened.” The process control and traceability of any deviation from the norm are vital to satisfying your needs.
Higher efficiency in many areas, whether it’s troubleshooting or process control. Failures due to an unstable furnace atmosphere can have grave consequence in the powder metallurgy sintering process. Now, instead of finding out several hours later via metallurgical analysis or physical measurement, your supplier can course-correct instantly and isolate any suspect product.- A predictive maintenance tool, rather than hoping your supplier reacts properly. Fewer delayed orders.
Enterprise Resource Planning (ERP)
Right now this technology is a standalone system. Where metallurgists can really increase its power is to integrate it directly into manufacturing cloud software such as Plex Systems. Use of this ERP software is one of the many improvements we’re making as the powder metallurgy industry becomes one with Industry 4.0.
To receive a more satisfying return on your partnership with a powder metallurgy company, work with someone who’s committed to both continuous improvement and Industry 4.0 best practices -- like using Plex. Click below to view a case study of how Plex’s platform and Horizon’s dedication to traceability have improved customer success: